
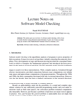
Ladle refractories were subject to repeated chemical erosion and physical scouring by various hot fluids such as steel slag, liquid steel, argon and oxygen. Firstly, the heat transfer model of ladle wall was established, the heat transfer of ladle refractory under different corrosion conditions was analyzed. The relationship between the residual thickness of ladle lining refractory and the temperature field of the outer surface of ladle was established. Secondly, a set of infrared thermal imaging ladle outer wall temperature monitoring system was used to measure the ladle outer wall temperature, especially the slag line temperature. The changes of ladle outer surface temperature field under different corrosion conditions and different process conditions were analyzed. Finally, based on the support vector regression (SVR) model, the residual thickness prediction model of ladle refractory was designed. Combined with the ladle surface temperature and steelmaking production process conditions, the residual thickness of ladle refractory corrosion was predicted. The experiment results showed that the prediction accuracy of ladle refractory corrosion reaches 92%, which met the requirements of steelmaking plant for ladle safety monitoring in green and intelligent production.