
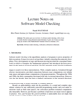
Through the observation of microstructure and crack morphology, the crack properties and causes of F92/Super304H dissimilar steel welding joint filled with ERNiCr-3 wire was analyzed. Results show the crack was distributed along the crystal and located between dendrites or subcrystals in the center or near the center of the 4th and 5th weld layers. Both dendrites with consistent direction and crystal cells formed on the free solidification surface can be observed on the crack surface. The crack can be identified as welding solidification crack because of its typical morphological characteristics of weld metal solidification crack. The reason for the crack was the weld width of the 4th and 5th layers with 16 ∼ 21mm and one weld bead for each layer. The wide weld bead caused the weld metal to stay at high temperature for a long time, and the weld metal generated coarse and developed dendrites with consistent direction. Elements such as Ni, Nb, Si and Ti have segregated between dendrites or subcrystals to form low melting point eutectic such as Ni-Nb and Ni-Si. Cracks were generated along dendrite grain boundaries or subcrystals because of the effect of solidification shrinkage strain. The inherent solidification crack sensitivity of nickel-based welding material and the factors of welding process were the main reasons for the crack.