
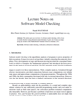
Although it is not uncommon to have a predictive model of a factory, these models are often simplistic in nature. Such models rarely reflect the current operating performance of the system, use simple and separate data streams and do not go down to machine/workstation resolution. They can support production scheduling, but typically they are of limited use for optimising factory performance in response to changing external stimuli. The industrially led research project OPTIMISED develops a holistic factory management platform to react quickly and efficiently to unanticipated disruptions to the factory. The project consortium consists of 10 partners from various disciplines. The project develops three industrial demonstrators in three different domains. Strengths of this research project include the high technology readiness level of its demonstrators and their application with real data at an industrial scale. This paper presents the application of simulation-based optimisation to support production scheduling of the manufacturing process of one of the industrial demonstrators. The simulation model captures all relevant production constraints of the factory down to each machine and work station. The simulation model reads data from business information systems, live data from machines and data from retrofitted sensors on the shop floor. The optimisation uses the simulation model as a fitness function. As a result, both service level and production costs are optimised. The paper highlights the main characteristics of the solution, its application in real industrial usage scenarios and some of the main conclusions and opportunities for future research identified during its development.