
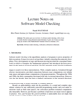
The steel leakage rate of tundish crucible during the preparation of superalloy powder by argon atomization pulverizing furnace in a factory was high, based on the systematical analysis of tundish crucible rupture engineering batch data, the key reasons of causing defects were found by six sigma method: the kind and the thickness of tundish crucible. The improvements were established after mechanism analysis and binary logistic regression calculation and so on. It was found that the Al2O3 sintered tundish crucible performed better than the MgO isostatic pressure forming crucible according to its better internal quality and compressive strength during producing superalloy powder in argon gas atomization furnace, in addition, the wall thickness of Al2O3 sintered tundish crucible was controlled between 8.0mm and 9.1mm, which was more beneficial to reduce the steel leakage probability. Hence, these measures made the steel leakage rate of tundish crucible reduce from 5.7% to 0.4% and the six sigma level of the preparation of superalloy powder by this argon atomization pulverizing furnace increase from 1.6 to 2.7. The production cost was greatly saved and the mass production of key parts for the advanced aero engines was stably ensured.