
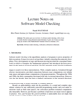
In semiconductor manufacturing, the process of manufacturing various components and wiring on silicon wafers requires high cleanliness. While traditional magnetic levitation slider devices are effective in preventing mechanical contact and minimizing dust generation, the suspension and propulsion mechanisms are often separated which can lead to inefficient use of vertical magnetic force. This research presents a new type of bearingless slider that integrates magnetic levitation and propulsion mechanisms through the utilization of a shared magnetic flux from an E-shaped iron core. This configuration maximizes energy utilization while minimizing energy loss caused by the separate use of suspension and drive devices while simplifying the overall structure. The stable point of the slider during the suspension process was analyzed using the finite element method. A dynamic model was developed, and suspension experiments were conducted to validate the model. The device can restore stable suspension within 3 seconds after being subjected to a 1N impact load during driving. The results indicate that the suspension system has good response characteristics and anti-interference characteristics.