
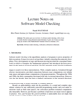
This study successfully develops a 7-axis suspended robotic arm for an automated spraying system, considering factors such as flexible operation modes, spray area dimensions, workpiece geometry, and the degrees of freedom required for effective operation. By using SolidWorks software for verification, the endpoints of the robotic arm can reach all positions within the workspace. The design and fabrication of the arm are completed according to specifications for structural strength, load capacity, rated torque output, and rotational speed. Kinematic analyses, both forward and inverse, are applied to determine the posture and position of the 7-axis robotic arm, facilitating the planning and design of the spraying trajectory. The control system architecture utilizes a multi-axis servo control board, integrated with a manifold deformation control method for trajectory tracking. Simulations and experiments are conducted to use a car shell workpiece provided by the manufacturer. The results from the simulations of MATLAB analyses show that the maximum tracking error is less than 0.4 mm. In experiments with the robotic arm, the maximum error is less than 0.7 mm. The results of the simulation and experiment are quite close, indicating that the deformation control method effectively operates the posture and movement of the 7-axis suspended robotic arm. Therefore, the 7-axis suspended robotic arm developed in this study will be effectively utilized in the production line of the automated spraying system.