
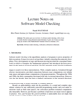
Given the weight and corrosion resistance limitations of traditional steel gas cylinders, this study proposes the use of lightweight, high-strength, and corrosion-resistant aluminum alloy as an alternative material. The research specifically focuses on analyzing the impact of winding technology and materials on the stress and strain of the gas cylinder at different temperatures (600°C) and pressures (from 15Mpa to 22.5Mpa), with the aim of optimizing the design and manufacturing process of the gas cylinder to meet more stringent engineering requirements. The study indicates that under high temperature (600°C) and high pressure (15Mpa) conditions, Type B gas cylinders exhibit lower average equivalent stress (573.66Mpa) and average stress intensity (589.36Mpa) compared to Types A and C. The average deformation is 0.01313m/m, slightly higher than that of Type C, but overall, Type B performs better. When the gas cylinder’s volume increases, the average equivalent stress, stress intensity, and equivalent elastic strain all decrease, albeit with relatively minor overall changes. When the temperature rises to 1000°C, the average equivalent stress reaches 927.96Mpa, reflecting the impact of temperature on material expansion and internal stress. These findings are of significant practical importance for guiding the future design and manufacturing of high-pressure gas cylinders to meet higher performance and safety requirements.