
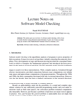
Thermomechanical fatigue is one of the most common cause of the failure in microelectronic technology in the solder joints. The lifetime prediction for microelectronic components is a very important area in nowadays automotive industry, because the lifetime estimation fatigue models in the literature differ in their results by orders of magnitude. However, developing an accurate lifetime estimation methodology for microelectronic components is not straightforward, because the failure mechanism of the solder joints under cyclic thermomechanical load is not fully understood. In addition, there are numerous tolerances and uncertainties during the designing and manufacturing processes, such as component size, copper pad area, solder material volume or the formed standoff height of the component from the copper pad. These parameters can hugely affect the lifetime of the solder joint. In this paper a benchmark analysis based on finite element method were carried out with four plastic strain-based fatigue models to understand the impact of the standoff height to the estimated lifetimes. Three CAD models were created with identical parameters, except the standoff height of the components. Creating the solder geometries for the 3D models, Surface Evolver software were used. The result shows that the fatigue models give the same tendencies varying the standoff height values. However, changing the standoff height increases the differences between models, even if they are tuned so that the estimated lifetime matches for a certain standoff height.