
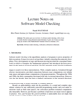
Manufacturing is becoming increasingly complex as product life cycles shorten, and new disruptive technologies are introduced. The increased complexity in the manufacturing footprint also complicates industrial decision-making. Proposed improvements to alleviate bottlenecks do not guarantee effective problem resolution. Instead, improvement efforts can become misguided, targeting a bottleneck that affects a single production line rather than the entire site. An effective method for identifying production issues and predicting system performance is discrete-event simulation. When coupled with multi-objective optimization and multi-level modeling, production performance issues can be identified at both the site and workstation levels. However, optimization studies yield vast amounts of data, which can be challenging to extract useful knowledge from. To address this, we employ data-mining methods to assist decision-makers in extracting valuable insights from optimization data.
This study presents an architecture for a decision support system that utilizes simulation-based optimization to continuously aid in industrial decision-making. Through a novel model generation method, simulation models are automatically generated and updated using logged data from the manufacturing shop floor and product lifecycle management systems. To reduce the computational complexity of the optimization, model simplification, varying replication numbers, surrogate modeling, and parallel computing in the cloud are also employed within this architecture. The results are presented to a decision-maker in an intelligent decision-support system, allowing for timely and relevant industrial decisions.