
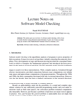
Production systems of the future may be in constant flux and reconfiguration, continuously adapting to changing production conditions. Digital models and simulation are powerful tools that can be used for their design and operation. These models must co-evolve with the physical system to sustain their usefulness and relevance. This poses a significant barrier, given the complexities involved in their efficient creation and maintenance. To understand whether certain system design concepts make the simulation process easier, this study aims to investigate a combination of concepts that promote reconfigurability and flexibility to explore whether they can positively influence the simulation process. By integrating modularization, interface standardization, and a service-oriented architecture it is believed to support faster and easier creation and updates of digital models. Modularization enhances flexibility by decomposing complex systems into independent, interchangeable modules. Standardizing interfaces ensures uniformity and compatibility among modules. Using a service-oriented architecture entails the encapsulation of various functionalities within modules as services, which can be dynamically requested. Shedding light on the advantages arising from modeling and simulating systems adhering to the mentioned concepts the research also aims to lay the groundwork for further investigation into the potential synergies of these promising production concepts. The study’s methodology includes modeling and programming of industrial robotic production modules adhering to predefined physical and logical interfaces. Interoperability and service orchestration are achieved through a service-oriented architecture. A simulated Manufacturing Execution System is integrated to facilitate handling of module services, product data and service requirements. Finally, a specialized software plugin was developed to support rapid module instantiation into a production system for evaluation. Results suggest that using a modular approach may ease modelling and simulation efforts and could be supported further by developing tailored tools for rapid system development.