
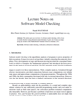
A continuously growing and mutating market with increasing demands on environmental sustainability, illuminated by unraveling environmental threats, highlights the need for greater resource efficiency in modern manufacturing industries. Machining has become pivotal in the pursuit of sustainability given its superior efficiency in manufacturing of metallic products.
In theory, the efficiency of a machining operation is dictated by the material removal rate and chip formation behavior. However, this may also present additional challenges as chips can be difficult to evacuate from the workpiece, and cause chip carryover. Chip management aims to contain manufacturing costs by addressing this issue and simultaneously pursuing higher machining efficiency. Persistent chips trapped in internal cavities is particularly challenging and can affect quality, and result in costly re-manufacturing, scrapping of portions of produced volume. Effective chip management strategies is therefore crucial to avoid these problems.
While there is established research on machining theory and chip removal, proposed solutions are often focused on a specific implementation and lack a holistic perspective on the phenomenon. This study aims to fill this gap in the knowledge by providing a strategic and practical application to tie together information that would otherwise be disaggregated. A case study was conducted to investigate the role of machining, and identify the source of chip carryover and its effect on subsequent production stages. Practical verification demonstrated the effectiveness of the proposed interventions in reducing production costs by decreasing the cycle time and reducing waste, and improving product quality. The future of sustainable manufacturing processes relies on the adoption of strategies and interventions that contribute to the efficiency and sustainability of the manufacturing industry. This study provides a valuable contribution to this effort.