
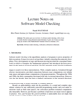
Peek is a special polymer material known for its exceptional mechanical properties, stable chemical properties, high temperature resistance, self-lubrication, wear resistance, and fatigue resistance. Peek is extensively used in various fields such as aerospace, automotive, electrical and electronic, and medical equipment. It has emerged as the most popular high-performance engineering plastic due to its excellent properties and versatility. Therefore, it is crucial to investigate the impact of process parameters on the quality of peek materials. This research article presents a finite element model that investigates the impact of process parameters on compression moulding density. The model incorporates the compression equation and the Shima-Oyane yield criterion. The model was used to perform finite element simulations of compression moulding with different process parameters. The simulation results show that increasing the compression load within a certain range enhances the top punch’s ability to overcome the interaction and friction between materials, resulting in increased forming density. By extending the holding time and improving the lubricant conditions, it is possible to not only increase the forming density, but also enhance the uniformity of distribution. This study lays the foundation for optimizing pressing process parameters and predicting future moulding results.