
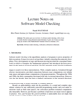
For achieving zero discharge of desulfurization wastewater, the 2×1,000MW Unit of a power plant in Hunan adopts the process of “low-temperature flue gas evaporation and concentration+high-temperature flue gas bypass drying and curing”. The heat source of the low-temperature concentration tower comes from the flue gas (97°C) after the induced draft fan, for direct heat exchange in the tower through counter-current spraying of desulfurization wastewater, with the concentration ratio of 4 or above. The high-temperature flue gas bypass drying tower extracts high-temperature flue gas in front of inlet of the air pre-heater, and process the concentrated solution in the rotary atomizing and drying tower for zero discharge. This paper focuses on studying the thermodynamic calculation regarding the low-temperature flue gas evaporation and concentration system and high-temperature flue gas drying and curing system, so as to establish a balance of quality and capability, and calculate the basic data for system design by the trial method. Meanwhile, it further studies the quantitative calculation of impact of the zero discharge system on thermal and economic indexes such as boiler efficiency and standard coal consumption. The maximum processing rate of each 1,000MW Unit can reach 13m3/h, requiring 13.61% of low-temperature flue gas. The high-temperature drying tower is designed to dry the concentrated solution at a rate of 6m3/h, requiring 1.73% of high-temperature flue gas. As a result, the temperature of flue gas at the outlet of the air pre-heater can be lowered by about 3°C, the air temperature at the primary and secondary outlets can be lowered by about 1°C, the boiler efficiency can be decreased by 0.066%, and standard coal consumption can be increased by about 0.183g/kWh.