
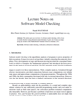
As one of the most important fracturing tools, the ball seat is widely used in the hydraulic fracturing process in the horizontal well. Due to the erosion of sand-carrying fluid on the inner wall of the ball seat, severe wear will occur on the surface of the material. This will lead to leak pressure and cause the fracturing failure. This study aims to investigate the erosion behavior of different ball seat structures and optimize the structure to increase erosion-resistant performance during the fracturing process. In this study, a two-section model of the ball seat combined with curved surface thought is proposed, and four models are designed. Based on the computational fluid dynamics (CFD) with Fluent software, four models are simulated and analyzed in actual working conditions using the dynamic mesh method with erosive wear deformation analysis for the first time. The simulation results show that the convex and concave curve surface structure has the lowest maximum erosion rate and most minor erosive wear deformation. Besides, from the point of view of pressure, research reveals the mechanism of different erosion behavior of ball seat structures and finds the optimal structure. Based on this structure, the curvature parameters are optimized by analyzing a set of models with different curvature. The results show that the optimal structure, convex and concave curve surface structure, with the 49 mm curvature radius of the convex curve and 57 mm curvature radius of the concave curve has the best performance to resist erosion wear. This research can offer a significant reference for structural optimization of the ball seat, simulation methods and prediction of the lifespan study of the ball seat.