
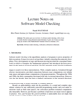
Cold Spray is an emerging technology in the domain of additive manufacturing. It is a solid-state high strain rate material deposition technique. It uses a supersonic (2-4 Mach) impact of process gas (such as nitrogen or helium) to deposit micron-sized (1-100 μm) metallic or composite powder particles onto a substrate via a severe plastic deformation mechanism without any significant fusion. To have a successful deposition, the specific powder particles should travel above a material-dependent threshold velocity, which is called the critical velocity. The convergent-divergent nozzle is employed for achieving high velocities. The main objective of the current research is to study the flow visualization of two-phase titanium particle laden nitrogen gas in a simulated 2-D axisymmetric nozzle where particles are having a particle size of 25 microns, and to investigate the suitability of a specific set of cold spraying process parameters for the successful deposition of titanium powder using computational fluid dynamics. For the analysis, a two-equation realizable k-ε simulation viscous model was preferred due to its more realistic consideration of the cold spray process and reduced computational cost. Titanium powder particles will be successfully deposited using cold spray when operated at the precise set of process conditions on account of the average particle velocity observed at standoff distance higher than the critical velocity.