
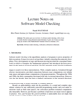
In the building of polymer-based composite high-speed marine vehicles, the designer has many more options than when building with equivalents of this material. The designer is faced with the possibilities of choosing a wide variety of fiber and resin materials, with the options for combining these materials almost endless. This width of the borders generally worries high speed marine vehicle designers, and with this concern, the designer tends to build heavy vehicles by using more materials than necessary to stay in a very safe zone. A heavy vehicle unfortunately does not serve sustainability, which is the main driver of designs today. In this study, the weight of the high-speed marine vehicle produced with such a design concern is improved by (1) optimizing the sequences of certain materials that the builders have established a strong supply chain, and (2) using today’s advanced composite material components, which the manufacturer has not used before. CFD methods and some rule-based approaches were used to calculate the pressures and accelerations around the hull. As a result of the analyses performed with the help of laminar theory and Tsai-Wu failure criteria, it has been seen that approximately 25% of the hull weight in the first way and almost 15% in the second way can be lightened. In light of the results obtained, suggestions will be made to marine vehicle designers for more sustainable building.