
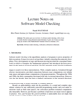
The hard phase added into the laser-cladding layer will be melted a lot with its size reducing or even disappearance because of rapidly heating of the laser beam with high power density during laser cladding, resulting in the properties of the laser cladding layer decreased. In order to regulate the hard phase size in the laser cladding layer, the surface modification of titanium carbide (TiC) by chemically clad cobalt (Co) was used to improve the expected performance after laser cladding. The mixing powder of Co-based alloy with the TiC powder of 40–60 μm, which the ratios among the Co-based alloy, Co-coated TiC and TiC powder are 7:3:0, 7:3:3, and 7:0:3, was clad to the surface of QT600-3 ductile iron substrate using a fiber laser, respectively, to obtain the cladding layer of 4mm thick by three sub-layers of cladding. Laser cladding process parameters are: laser power P=1.2kW, scanning speed of 320mm·min-1, spot diameter of 3mm, lap rate of 1.5 between two passes. The variation of the micro-structure, second phase and hardness of the cross-section of the layer was analyzed by Olympus metallographic microscope (OM), scanning electron microscope (SEM) observation with energy diffraction spectrum (EDS) and Rockwell hardness tester. The results show that the clad layer is well formed on the surface without cracks, pores and other defects and well bonded with the substrate. There exist a large number of TiC hard phases in the microstructure with a little difference of the TiC size compared with the raw material powder, because the melting of TiC under the laser beam is reduced after the TiC clad with Co. So, the hardness of the cladding layer was improved compared with the ratio of 7:0:3 and increased rapidly and then gently with the increase of the distance from the surface of the ductile iron substrate. Under the condition of 7:3:3 powder ratio, there appears a large amount of new dendritic TiC phase in the microstructure, where the grains were refined, and the maximum hardness of the clad layer was obtained with 64.5 HRC.