
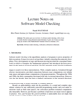
Marine diesel engines are systems integrated into a complex ship’s propulsion plant and comprehensive diagnostic analysis of possible degradations and failures is very challenging. Nowadays, current software and hardware allow exploring innovative ways, although each methodology cannot be considered apart from an adequate onboard monitoring system. In this work, the effects of several typical degradations of a ship’s engine, affecting some parameters that can be monitored on board, have been supposed and analyzed in order to their detection at an early stage by processing some parameters that can be monitored on board. The main aim is to provide a tool able to trace the engine performance decay. The procedure is based on the simulation of the engine model performed with input data measured on board and on a comparison of the outcomes with the real data. The case study is a 12.000 kW (750 rpm) 4-stroke marine diesel engine, simulated in a Matlab/Simulink environment and validated through the manufacturer’s datasheet. At this stage of the research, to make up for the lack of experimental data recorded onboard, a more detailed engine simulator is used to generate onboard data, with some alterations of the operating conditions as, intercooler efficiency and loss of pressure, turbocharger fouling, and many others. The numerical diagnostic tool acts on the minimization of the mean square errors (optimization problem) between the measured and the numerically simulated engine variables (such as pressures, temperatures, etc…) by properly varying the model parameters. The state of the engine is evaluated by analyzing the offset between the parameters of the degraded model and those obtained through the identification procedure for the degraded case.