
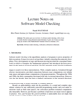
For the needs of gripping and transferring and assembling thin-walled fragile parts in industrial production, an internally supported manipulator configuration with finger-palm synergy features for thin-walled brittle cylindrical inner workpieces is proposed. Due to the poor impact resistance and low tensile strength of brittle materials, they are easily broken during the manipulator operation. In order to find the internal brace gripper finger configuration and stiffness matching for the operation of thin-walled fragile parts, and to explore the contact-collision law of the gripping process, the finite element model of the mechanical finger end parts was established by the integrated modeling method of Hypermesh and other software, and the change of the internal force of the mechanical finger contact with the workpiece when the gripping impact speed changes was studied. The corresponding constraints, loads and contact types are applied to the finite element model by LS-prepost software, and post-processing is performed to calculate the stress and strain clouds during the contact collision of the fragile parts. The simulation results show that the stress on the fragile part increases linearly with the increase of the impact speed of the manipulator: Under the speed of 4 mm/ms, the stress increases linearly and slowly. When the speed goes from 0.5 mm/ms to 4 mm/ms, the stress increases about 8 times in X, XY direction and about 14 times in Maximum Principal, Y direction. Above the velocity of 4 mm/ms the stress increases sharply and the model is destroyed. The results of the study establish the basis for optimizing the manipulator’s operating process.