
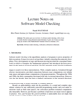
Production systems are evolving rapidly, thanks to key Industry 4.0 technologies such as production simulation, digital twins, internet-of-things, artificial intelligence, and big data analytics. The combination of these technologies can be used to meet the long-term enterprise goals of profitability, sustainability, and stability by increasing the throughput and reducing production costs. Owing to digitization, manufacturing companies can now explore operational level data to track the performance of systems making processes more transparent and efficient. This untapped granular data can be leveraged to better understand the system and identify constraining activities or resources that determine the system’s throughput. In this paper, we propose a data-driven methodology that exploits the technique of data integration, process mining, and analytics based on factory physics to identify constrained resources, also known as bottlenecks. To test the proposed methodology, a case study was performed on an industrial scenario were a discrete event simulation model is built and validated to run future what-if analyses and optimization scenarios. The proposed methodology is easy to implement and can be generalized to any other organization that captures event data.