
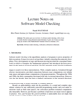
The manufacturing industry faces the challenge of providing copious product variety at a competitive price. This development has escalated into the point where SMEs are becoming in need to consider product mix as a relevant aspect for automation selection despite low volumes. Apparently such a manually operated production cell has productivity limitations in addressing these increasing demands of mass customization and competitive prices. Therefore, this paper proposes using discrete- event simulation (DES) to assist the decision-making process (DMP) for implementing a new automation technology within a production cell and showcase key performance indicator (KPI) identification using simulation. Two modeling scenarios were designed and contrasted to showcase implementing automation. One consists of a manually operated assembly line, and the other represents a semi- automated assembly line of the same process but with robots in specific areas of the production line. The results indicate that the comparative study between the two scenarios of a manually operated assembly cell and a semi-automated one can provide valuable insights into the DMP. The proposed approach has shown several influencing factors to consider in the DMP. The choice of prioritizing which element should have precedence depends on the requirement specifics. The insights from the study also indicate the requirement of further research in this context, considering different parameters apart from the current research and understanding their influence on the DMP. Moreover, acknowledging the secondary aspects concerning this study context, such as ergonomics, space utilization, workplace safety, and sustainability, require further investigation.