
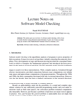
Nowadays customer needs are changing rapidly, resulting in shorter product life cycles and a need for a higher product introduction rate. This requires manufacturers to introduce new products whilst keeping production efficiency at a satisfactory level and production costs low. Based on these challenges, there is a need to consider both production efficiency and potential assembly line investment costs during the planning of new product introductions. Hence, this paper aims to support decision-making regarding whether to introduce and produce a new product in an already existing assembly line or to invest in a new assembly line. To its support, a tool which illustrates how to support manufacturing investment decisions through line balancing techniques has been developed. The tool was based on theoretical findings from two literature reviews, investigating assembly line balancing techniques and assembly line investment costs, and through data collected in a single case study, including how a company is currently supporting investment decisions and performing line balancing. The case study was conducted with a large Swedish company from the automotive industry. Data was collected through semi-structured interviews, document studies and a focus group. The proposed decision-supporting tool conducts line balancing for both combined and separate assembly lines, and converts the results into costs. These costs are then compared with the potential investment costs of either producing in an already existing assembly line or investing in a new assembly line. The final output is a summarization of the potential costs related to both alternatives which provides the user with the most economically beneficial alternative by taking both production efficiency and investment costs into consideration.