
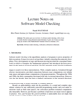
With the development of science and technology, magnetic suspension products are gradually favored by people for the characteristics of no friction and wear, no lubrication and long life. With the increasing consumption of fossil energy, magnetic levitation green energy-saving equipment is gradually studied by researchers. Taking magnetic suspension flywheel (MSMFW) as typical representative, magnetic suspension products in aerospace field have been greatly developed. As the core component of magnetic suspension flywheel, magnetic levitation motor has been widely studied. To obtain the better performance of magnetic levitation motor when it was used in magnetic suspended momentum flywheel, the motor rotor system structure was optimized in this paper. Firstly, the rotor system moment of inertia was calculated and analyzed, and the optimum ratio of polar moment of inertia to equatorial moment of inertia was obtained. Then the basic structure of motor rotor was designed on the basis of the rotor system dynamic analysis. Thirdly, based on the flywheel motor system model, the ANSYS Parametric Design Language (APDL) file was established, and it was applied to optimization software ISIGHT to complete the optimization. In the optimization process, the design variables boundary conditions were given, and the Sequence Quadratic Programming method was used for maintaining the optimization process and the optimization convergence results was obtained. The magnetic flux density as the optimization objective is increased from 0.393 T to 0.53 T through the optimization, which is 34.9% larger than before. It is of great significance for the magnetic levitation motor design, and the engineering application of magnetic levitation motor based on optimization results will be done in the future.