
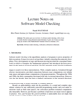
Motion control of rotational moulding is an area which has not been extensively investigated beyond the current trial and error approach. Different motion control schemes will lead to varied powder flow regimes which exhibit different levels of mixing and temperature uniformity. Rotational moulding is hampered by long cycle times. Choosing the ideal rotational speed should allow the optimum use of the inputted heat energy to cause all of the powder bed to become ‘tacky’ and adhere to the mould wall in the shortest time period. This paper investigates the hypothesis that the optimum rotational speed should be chosen by considering the flow regime of the powder bed at the bottom of the mould, in order to reduce manufacturing time and energy consumption. Experiments were completed to validate this approach using a cylindrical mould under uni-axial rotation. Results show that the ideal rotational speed is found when the powder is flowing in a rolling regime and suggests that further cycle time savings could be achieved by varying the speed during the heating cycle. The effect of rotational speed on part quality (wall thickness uniformity) was also investigated.