
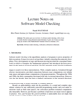
Reducing machining time is one of the ways to improve the global competitiveness and productivity. The objective of this paper is to optimize feedrates of milling operation via process modeling, numerical experiments, and an intelligent algorithm under multiple constraints. The approach proposed attempts to overcome drawbacks of human error and computer-aided manufacturing (CAM) software through efficient cutting parameters of given toolpaths. First, machining simulations were performed with the support of CAM system in order to generate the NC program. The milling process was analyzed and re-simulated using the experimental platform to calculate material removal rates and instantaneous forces at the specific time. To obtain the machined accuracy, a new mechanism for milling process has been considered. The cutting force and acceleration as well as deceleration time were considered as machining constraints and integrated into the developed system. The optimizing strategy is the feedrates scheduling, which increases the feedrates to an allowable level to make the process more efficient, taking into consideration the required constraints. Subsequently, an intelligent algorithm was proposed to find real-optimal feedrates and generate more-efficient toolpaths. Finally, machining simulations using optimal values were conducted to evaluate time saving potentials. The results indicated that machining time could be reduced approximately 22%, compared to un-optimal case. Consequently, this work is expected as a contribution to make the milling process more efficient