
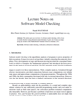
In grinding it is often desirable to have a control system that can utilise auxiliary Process Control and Monitoring equipment to perform optimised production cycles either using manual (operator) or automatic (CNC) intervention. Implemented functions include wheel balancing, in-process gauging, and touch detection (via acoustic emission and wheel power monitoring). These units can be separate and from different manufacturers, or an integrated subsystem from a single supplier. For optimised machining (including Adaptive Control) the monitoring equipment should be tightly linked to the machine control, with signal states and data values being easily available for action and analysis. It would therefore be highly beneficial to provide for the use of process monitoring equipment as part of the fundamental machine control design. Many elements of the machine and control system – such as the operator control panel and the axis movement or motion control features – can be considered as objects or devices with comparable structures but differing characteristics. If external monitoring equipment is similarly treated as a generic device configured as part of the machine via a standardized interface, its integration and operation can be simplified considerably. A generic software structure abstracts the underlying details of a device's implementation and allows simpler incorporation of additional functionality to the machine. This paper reports on the design and implementation of a grinding machine controller with an Open Device Interface (ODI) software framework that connects a variety of monitoring units to the machine process control.