
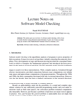
While striving to mitigate the risk to human health and the environment, chemical substance regulations continue to impose greater legislative burdens on industry, which ultimately creates business continuity risk. Compliance to these regulations requires greater investment which ultimately undermines profits. Furthermore, as regulations vary between countries or politico-economic unions, impact on manufacturers is dependent on which areas of the world that its supply chain is most prevalent. A chemical substance reporting system for manufacturing companies requires information on parts and manufacturing processes that are both defined in-house and within the external supply chain. Without information on chemical substance uses within the downstream supply chain, manufacturers cannot fulfil their legislative obligations or effectively manage business continuity risk. Often the biggest hurdle to collecting this information is supply chain engagement, which is made more difficult with multiple, different industry standards and data exchange formats. As more and more chemical substances become heavily regulated, manufacturers require increased volumes of downstream supply chain information on a routine basis. The aim of this paper is to identify existing good practices which could be utilized to implement chemical substance reporting systems for manufacturing companies.