
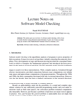
The robust engineering and many related engineering applications are seeking for design of products and processes insensitive to changes in the work environment as well as to variation of the components. At the individual type of production the basic function of the product and the main design solutions are generally known, but a unique product is assumed to have its own details that require the respective individual design approach and have a direct impact on both, the design process as well as on a later production process. Such an industrial environment is very specific, therefore robust construction process plays a key role in the final value of the product. The robust process has built-in mechanisms to detect potential errors on time, to eliminate them and to initiate all the necessary measures to ensure the same error does not occur again. Implementation methodology of these mechanisms is essential, as it should provide cost-effective and useful engineering solutions. The sample company is engaged in the development and production of large power transformers. Based on a systematic analysis of current development and design process we propose a multi-level, systematic approach for a complete renewal of system information and working methodology, where reorganization of activities are anticipated to result in an increase of overall effectiveness. The paper presents the key preliminary findings and deals with answers of how to analytically manage individual segments of design process in order to achieve optimal conditions for individualized construction process. At the end the instructions for the implementation of improvements as well as recommendations for further activities are given. The final aim of the research is to implement the identified solutions in a real-world industrial environment, to obtain their approval and finally to establish a generalized model of support processes for individual production.