
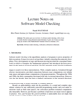
This paper aims to present the importance to create a new and lean process for identifying potential failures during development of complex products. It has been identified in the literature and in companies the lack of knowledge to select the most appropriate quality tools in order to solve and or prevent the potential problems that might appear during the prototype development and launching phases of complex products. Literature about quality tools are easily found, therefore there is much questioning on the appropriate quality tools to be selected and how, where and when they should be applied. Based on this, this article aims to provide the understanding of the quality tools during program development and direct their application (Design for Six Sigma, Design FMEA, QFD, TRIZ, Robust Engineering, DFM and DFA). It is noticeable that even applying quality tools during all phases of complex products the failures still exist and, therefore, still cause a lot of problems to the companies that can be letal (example: at aerospace, automotive, metallurgical, medical and others companies) (CANCIGLIERI, OKIMURA, 2015) [1]. Besides all this, this paper will provide the evidence that something in addition to quality tools application should be done to guarantee design robustness of complex products. Two case studies provide evidences that only performing quality tools analysis like Design FMEA, DFSS, DFM, DFA and others is not enough to achieve the objectives of quality, as well as competitiveness, that large companies are looking for. A new and lean process is necessary to evaluate and identify the failures in a robust and definitive scenario. The new processes is based on the concept of Lean System Engineering as well as Lean Engineering Principles and propose to create a dual process to the systems engineering process mitigating the risks of failing what should be done as planned in the product and its life cycle processes.