
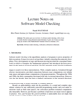
This paper assesses the impact of various eddy current probe parameters in terms of the probe's crack using Wyle's fully automated Eddy Current Inspection Station (ECIS). Probes were manipulated by the ECIS to simulate a certain coil orientation, rotation, or tilt then scanned and indexed across 15 × 8 × 3 mil EDM notch for calibration. Following calibration a set of fatigue cracks ranging from 3 to 23 mils in depth were inspected in both transverse and longitudinal (in-line) orientations with respect to the scan direction with indexing consistent with calibration. Layers of tape were also added to the probe shoe to simulate liftoff, and a potentiometer was added in series with the drive coil to vary the field produced by the drive coil. Drive frequency was varied to assess the system response as a function of drive frequency, and probes of various degrees of imbalance were used to assess the impact of probe balance. For all tests the gain calibration sensitivities were recorded and used to normalize crack responses to effectively obtain un-calibrated crack responses. Calibrated and un-calibrated results were then compared and the experimental results were analyzed and reported. Some work was done to evaluate possible techniques to compensate for various critical probe parameters, but that work will be the topic of a future paper.