
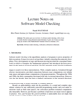
Trends in the automotive industry tend towards fuel saving and reduction of exhaust gases by weight reduction. On the other hand the enhancement of safety is required. From this it follows an increased application of high strength steels as well as stainless steels in the car body production. The forming of these materials is associated with high requirements to forming procedure and forming tools. In comparison with forming of low strength steels the risk of spring back effects is increased caused by higher amount of elastic deformation. Furthermore during deep drawing processes tearing nearby the die corner may occur because load strengths in this area are too large. These load strengths are so called “plane strain” states.
In order to avoid or reduce failure a monitoring of the stress states during the deep drawing process should be implemented. Basically the non-destructive electromagnetic testing method 3MA (Micromagnetic Multiparameter Microstructure and Stress Analysis) is convenient to characterize stress states. A special miniaturized electromagnetic probe, a so called rotating field probe, which is able to detect multiaxial stress states, was developed.
In a first step measurements in a cross tensile test, which allows the generation of the critical “plane strain” state, were performed. Systematic dependencies between the electromagnetic signals and the strain states could be observed. Based on these measuring results the rotating field probe was integrated in a deep drawing tool. During the deep drawing process changes in the strain states could be detected nondestructively for the first time.