
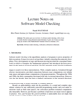
This paper concerns the operation of the actuator for a prototype micro-engineered mechanical palpation device for deployment via a cystoscope to measure the dynamic mechanical properties of the prostate gland in vivo. The subassembly consists of a 400×200 μm silicon (Si) piston manufactured using deep reactive ion etching (DRIE) housed within an anodically bonded glass-Si-glass sandwiched housing. The micro-channel on the Si layer was formed by powder blasting and contains the micro-piston with one end pointing to the side of the housing and the other facing a via hole leading to a capillary tube. The opening on the side of the housing was sealed by a 5 μm thick silicone membrane which acts to retain the micro-piston and act as a return spring. A 320 μm diameter capillary forms the connection between the micro-channel and a micro-syringe which is operated by a programmable syringe pump to produce a reciprocating action. A pressure sensor is connected along the capillary tube to measure the dynamic pressure within the system. The micro-piston has already been used, separately actuated to measure the dynamic mechanical properties of known viscoelastic materials and prostate tissue. The purpose of the present work is to assess the functionality of the actuator assembly.