
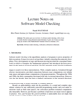
Soon after the landmark paper by Scott White and colleagues [1] demonstrating the concept of autonomous self healing in a man-made material, materials scientist in the Netherlands realised that the concept of self healing is not restricted to brittle polymers, but can be applied to all other classes of materials. This realisation was based on their conceptual insight that self healing requires the creation of ‘local, temporary mobility’ in an otherwise regular material [2]. In the Scott White concept, the material to be turned into a self healing grade was an existing regular high performance epoxy for aerospace applications. The ‘mobility’ was created by the use of a liquid healing agent (liquids being mobile by their very nature). The ‘local’ condition was met by encapsulating the liquid healing agent. The condition ‘temporary’ was also met as the liquid only was able to flow in the period between the crack opening the capsule and the onset of cross-linking upon contact with the catalytic particles dispersed in the matrix. As we all know, the concept of local temporary mobility also works in nature. If one's skin is cut, blood will temporarily be able to leave the veins and to flow into the cut. Once in direct contact with air, the blood will rapidly cross-link and the liquid blood becomes a flexible (non-flowing) gel which over a number of successive chemical reactions turns into new skin. Self healing of bones in a human body works in a similar way. First, there is a flow of electrolytes and proteins from the surrounding tissues to the fracture surface. Then, a bridging polymeric gel containing a high proportion of inorganic particles is formed, which in turn is transformed into new bone with a new microstructure to compensate for the loss in original optimised macrostructure. We also know from nature that healing does not occur in all cases: broken teeth just do not heal. To make our teeth function optimally they must be hard and sharp and not react to any food we may eat. Hence, in teeth the bone structure is very dense (not allowing space for microscopic flow) and chemically very stable (not allowing new bonds to form).
The above examples all deal with flow of a liquid-like substance over microscopic dimensions, but the concept of local temporary mobility is generic and can be applied at different length scales. In some self healing polymers that are capable of multiple healing, weaker (reversible) molecular bonds break sacrificially while keeping the polymer backbone intact. The dangling chain ends move around for a certain time in the vicinity of the fracture surface and then they recombine with dangling chains from the opposing fracture surface and lose their mobile state.
The challenge of creating self healing materials is not to create a totally new material (like CNTs and graphene being new materials) but to modify existing materials such that upon local fracture or scratching, they autonomously (or upon a slight stimulation) restore their prime functionality, be it mechanical strength and stiffness, water impermeability, corrosion protection or surface friction or any other functionality. Self healing concrete is essentially like any other concrete with all its good and bad properties, but with the added ability to heal cracks. Self healing creep steels are like any other creep steel with all their good and bad properties, but with the added ability to heal creep damage as it forms. Self healing organic coatings are like any other organic coating with their usual processing and properties characteristics, but have the ability to restore adhesion to the substrate and restore the corrosion protection of the underlying metallic substrate.
So, to make a material self healing, material designers only have to focus on how to create the three requirements local temporary mobility and to respect the ‘natural’ character of the material [3].
It is important to point out the fact that the three key concepts local temporary mobility already imply that healing will never be instantaneous, but will always take time. The healing ‘agent’ will have to ‘flow’ to the damage site, it has to interact with the crack faces and it has to ‘transform’ from a mobile state into a more solid state. This all will take time. The actual amount of time will depend on the nature of the material as well as the prevailing conditions. Healing of fractured bones takes typically 6 weeks as the deposition of the new organic-inorganic material in the crack is relatively slow. The net material transport rate is low and the conversion of the temporary flexible gel-bone structure into the strong, more rigid bone structure is a slow process too. In contrast, the healing of a cut in a human skin is relatively fast and typically occurs in 1 to 3 minutes. The short healing time is due to the rapid and abundant supply of blood through the veins in combination with a fast gelation of blood upon exposure to air. As we all know, the healing time also depends on the size of the cut. Small and superficial cracks take a shorter time to heal than deep and wide cuts. The healing time also depends on the prevailing conditions, just as in nature: while a healing time of 1 to 3 minutes for a skin cut is acceptable, healing of a cut in a tongue is a lot faster. The biological conditions in the mouth promote rapid and non-scar-forming repairs. The mobility aspect means that healing does not only depend on local chemistry but of course also on temperature. Routes which work well at room temperature may not work so well under arctic conditions, and routes which do not work so well at room temperature may work well at high temperatures. Finally, the healing time should always be seen in the context of the application. For restoring fluid containment after ballistic penetration a fast healing reaction in the sub second regime is required. For concrete buildings with an expected life time of 40 years or more, the healing may take longer and a healing time of weeks may be adequate.
In an ideal case, the self healing process would be truly autonomous, i.e. not requiring any human intervention and multiple successive healing events at the same damage location should be possible. Furthermore, ideally the new self healing material would have properties equal to those of the current non-self healing materials on the market. To make the wish list complete, the self healing material should have the same (if not lower) cost price as existing materials.
Let us first address the issue of reduction in property levels when turning a material into a self healing grade. In self healing materials we have to set aside a certain fraction of chemical bonds/atoms/molecules in the material in order to make it self healing. The mobile ‘healing’ bonds/atoms/molecules do not contribute to the principal mechanical or functional properties, and some reduction in initial properties is not to be avoided. However, in real applications it is not the material performance we want to maximise, but the performance of the product we want to make out of it. In designing a product constructed out of non-self healing materials, the designers and engineers apply a so-called ‘safety’ factor. This ‘safety’ factor takes into account the reduction in material performance due to the accumulation of unspecified damage during use. In case of an ideal self healing material, the damage is fully and perpetually healed and no safety factor is required. So, some reduction in initial properties is acceptable provided the loss in properties is less than that following from the application of a ‘safety’ factor [2]. There are numerous practical examples where self healing behaviour could lead to a product having an extended life time even if the initial material properties were lower:
– The Colosseum in the city of Rome would not be standing firm after more than 2000 years if the mortar used has not been self healing;
– A corrosion protective self healing polymeric coating would maintain the local corrosion protection even in case the coating was locally damaged by mechanical impact;
– Early failure in LED's would be prevented in case the thermal interface material connecting the die to the lamp structure would re-attach itself to both surfaces upon overheating due to local delamination;
– More slender concrete buildings could be constructed in case the concrete was self healing and moisture transport to the steel reinforcing structure was autonomously prevented;
– Pressure vessels in power stations would last longer in case self healing steels would resolve grain boundary pore formation and coalescence internally.
In all these cases it is not the performance of the undamaged material which is the limiting factor, but the response of the material and structure to unavoidable local damage.
When analysing the potential application fields for self healing materials, several fields of application can be identified. Most of them have a more secure performance of the product as a whole as the main driver for material change. The use of self healing materials is foreseen in applications where performance reliability after the occurrence of undetected minor damage has to be guaranteed (e.g. aircraft, ships, flood barrier constructions). Applications where a very long life is to be guaranteed under a spectrum of only partially known conditions (e.g. tunnels, bridges, conventional and nuclear reactors) are also of interest. While not always of structural relevance, in many applications a guaranteed high-quality outer surface (e.g. as in automotive exteriors and interiors, compact discs for data storage, glasses and optical devices) is highly appreciated and a factor making a crucial difference in the product appreciation. Finally, all applications where repair to local damage is costly and/or disruptive (such as sewage systems, sea-based wind turbine farms and motorways) would greatly benefit from self healing materials being available.
Finally, all new materials can only enter the market if the increase in performance outweighs the increase in cost. In this respect, self healing materials have an extremely high probability of entering the market. As stated earlier, self healing materials are essentially existing materials with an added functionality. In contrast to other novel materials such as diamond like coatings, room temperature superconductors, aramid fibres, fibre metal laminates carbon nanotubes and graphene, no new process and application technologies need to be developed. The processing of self healing polymer coatings and the processing of self healing concrete will in most cases require the same processing equipment as being used for their current non-self healing predecessors. The absence of a need to invest in totally new processing equipment will substantially reduce the introduction costs of the new self healing material grades. Of course, any material modifications to give new functionality will increase the material costs, as the complexity of the processing is likely to increase and the new modifications will generally not be as cheap as the base material. However, the increase in material cost in most cases can be kept at a relatively low level. Furthermore, in modern times, cost of a product, installation or piece of infrastructure at the moment of acquisition is no longer the dominant parameter. Material selection is increasingly made on the basis of a product life cycle analysis in which maintenance cost, life time extension, reliability issues related to early failure and end-of-live aspects play an equally important role as minimisation of the acquisition costs. A recent study on the pricing of a (very) low cost material (porous asphalt concrete for Dutch motorways) has shown that that a doubling of the bitumen cost to make it self healing would lead to a net profit of 20 MEuro per year if this would increase the life span of Dutch motorways by 50% [4]. Other studies (e.g. for self healing coatings for off-shore installations in the oil and gas industries) have shown an even much larger acceptable increase in cost price, provided the coating becomes truly self healing for a number of years.
Inspired by the scientific and technological challenges and the opportunities to create materials making products and installations last longer, at a lower maintenance cost and in a more reliable manner, a proposal for a programmatic study into the development of self healing materials was submitted in 2005 to the Dutch Ministry of Economic Affairs. The proposal was submitted by a consortium of academic experts working in the field of polymers, metals and concrete and several companies ranging in size from a multinational to a small company of less than 100 employees. The application was made in the context of the highly successful 25 year old Innovative Research Program (IOP) programmatic funding scheme of the Dutch Ministry of Economic Affairs. The aim of the proposal was to conduct pioneering research in the emerging field of self healing materials. The program differed from smaller programs outside the Netherlands by covering all material classes and not specifying the route to reach the self healing behaviour. In the proposal the consortium committed itself to transmit the key information on the new self healing material systems to the industry in such a manner that the new concepts would lead to new high-value products entering the market in record time.
The proposed IOP program Self Healing Materials was to be supervised by a Supervisory Board with members both from industry and academia. The research was to be conducted via projects each having one or more academic partners and at least two industrial partners per project. Professor Sybrand van der Zwaag (Delft University of Technology) was proposed as the director for this program. The total financial contribution requested amounted to 10 MEuro for a four year program with the option of an extension of the program for another four years and another financial contribution of the same magnitude.
The key element in the original IOP program proposal guiding the selection between the many high quality research projects submitted during the course of the program, was a table defining the distribution of the funds over the various material classes and types of activities. These percentages were the outcome of stimulating discussions during several preliminary workshops involving senior and junior representatives from companies, universities, the Ministry of Economic Affairs and institutes active in the field of materials science and engineering in the Netherlands.
As the table shows, a large share of the research funds (40%) was to be devoted to the field of self healing polymers. This was based on the notion that in comparison to other material classes, polymers have a much higher molecular mobility at room temperature and their processing conditions are generally milder. Opportunities were seen for both thermoset and thermoplastic polymers. The research was to focus both on extrinsic (i.e. the healing was to be realised via the addition of discrete encapsulated liquid healing agent containing entities) and intrinsic (i.e. the polymer molecule itself can heal the damage via reversible chemical or physical bonds) self healing approaches. The metals domain would receive a lower fraction of the funding (20%) as it was realised that self healing in metals would be difficult to realise. Due to the high melting point of metals the intrinsic mobility of atoms at room temperature would be very low. However, opportunities were seen for age hardenable alloys and creep resistant steels. Earlier work on self healing materials at the Delft Centre for Materials (Delft University of Technology) had identified some very promising leads to induce self healing in asphalt and concrete, so a relatively large fraction (25%) of the national budget was allocated to the domain of civil engineering materials. Finally, a substantial amount of funding (15%) was to go to the domain of fibre reinforced polymer matrix composites. The relatively high level of funding was based on the high added value of composite products. Furthermore, it was realised that the fibrous architecture of continuous fibre composites offered attractive opportunities to create long range transport of the healing agents. As to types of activity, most of the effort was to be devoted to the development of new concepts, yet it was widely agreed that substantial funding should go to the development of a theoretical basis and developing the computational framework. Much to the surprise of the Ministry and the senior academic administrators, the industry indicated that the financial commitment to application oriented research should be kept small. Intentionally, the fractional funding at cell level was left undefined, so as to give the Supervisory Board of the IOP the chance to build a coherent research program on the basis of the best and most innovative research proposals submitted.
At the mid-term point of the program a new priority table was defined, taking into account the lessons learned during the first four years of research.
Compared to Table 1, there were some significant changes in the grouping of materials to be studied as well as in the relative funding levels. It was found that the research on self healing composites had focussed almost exclusively on the healing of the polymer matrix. Hence, a new domain Polymers & composites was defined. The research on self healing in metals was found to be most successful in the field of high temperature metals (creep steels) and opportunities were seen to extend the field to high temperature ceramics. This led to the creation of a new domain Metals & ceramics, devoted to the healing of (bulk) metallic and ceramics. The domain of Civil engineering materials was left unchanged as it was found to function very well. While strictly speaking not a material class, Coatings were defined as an area of special attention. By their very nature coatings have an increased probability to become damaged due to external impact or mechanical loading. Furthermore, the presence of an unfractured substrate to keep the fractured coating surface in some form of topological registry offered an additional positive contributing factor. The inherent limited thickness of the coating presenting an additional constraint to the mass transport to the crack in comparison to healing of bulk materials. Research in the newly established coating domain was to focus on organic (polymer) coatings as well as on inorganic (metallic or ceramic) coatings. Finally, it was realised that there was an opportunity to open the field of self healing to Functional materials (i.e. materials which prime function is non-mechanical in nature, such a conduction of heat, emission of light or stimulation of an electrochemical reaction). To stimulate the research in this field, a new domain Functional materials was created and 15% of the budget was allocated to it. The apparent reduction in fractional funding for polymers and metals with respect to that in Table 1 was in part ‘administrative’ as both material classes were to be addressed in the domain Coatings. As to activities, more attention was to be given to the development of protocols for material testing and quantification of degree of self healing. Furthermore, in particular at the request of the participating industries, the research on theory and modelling was to be strengthened.
The IOP program financed 42 projects, involving 20 research groups located at 5 Dutch universities and no less than 68 companies. This book presents a highlight of the results obtained in the program. The chapters are structured along the domains defined in Table 2.
The first 9 chapters of this book all address research in the field of Polymers & composites. The section starts with a chapter on mechanochemistry of individual molecules in a polymer network and shows how fracture of a single molecule can trigger a catalytic reaction restoring the network again. The subsequent five chapters deal with various new polymer systems in which reversible chemical bonds are used to induce self healing behaviour. The new polymers are to find their way in the human body, or as robust elastomers for engineering and coating applications. These five chapters are followed by a chapter on the (only partially successful) creation of robust silica based capsules filled with liquid healing agents stable enough to withstand regular thermoplastic processing routes. The section ends with two chapters dealing with self healing in fibre reinforced composites. The first of these two chapters deals with a novel fibre concept for the storage of healing agents, while the other chapter deals with self healing in a composite structure involving the use of shape memory alloy wires to close the cracks formed.
The section Metals & ceramics contains 5 chapters. In the first chapter it is shown that under specific conditions dynamic precipitation at deformation induced defects can lead to a significant increase in the fatigue lifetime of aluminium alloys. The subsequent two chapters deal with research on extending the life time of steels by the autonomous filling of grain boundary cavities. It is demonstrated that both copper and gold are excellent alloying element to induce self healing in steels at temperatures as high as 550 0C. The final two chapters in this section focus on ceramics and deal with self healing behaviour at even higher temperatures. Significant advances in the wear resistance are reported.
While the previous sections contain chapters describe research on materials not yet ready to enter the market, the section Civil engineering materials contains 7 chapters dealing with research on both concrete and asphalt, spanning the entire range from lab scale experiments to real life field testing. The chapter also contains a numerical study on the rate of healing in bacterial concrete as a function of the microstructure and the crack dimensions. Models like these are crucial when re-designing and redimensioning real constructions on the basis of the self healing behaviour of the material. The two chapters on the prevention of frost damage in blast furnace cement and mortars describe more early stage work, but also they hold great promise for future applications.
In general, coatings are applied to provide various functionalities to different types of substrates and this diversity is reflected in the Coatings section. The section contains 6 chapters on the protection of wood by biofilms, self replenishing low friction polymeric coatings, self healing anti corrosion coatings on aluminium substrates and thermal barrier coatings on super alloys. Some of the work is still at its exploratory stage but the coatings for low friction, anti-corrosion and thermal protection are well on their way to commercialisation.
The book ends with a section on self healing Functional materials. Functional materials are materials which have different primary role than the handling of mechanical loads. The section contains only 3 chapters, yet describes truly pioneering research in the field of self healing in thermal interface materials for LED's and micro-electronic devices, layered organic light emitting diodes and catalytic nanoparticles in fuel cell membranes.
Finally, while this book shows the impressive range of results obtained purely in the context of this IOP Self Healing Materials program, the IOP program also initiated additional research together with Dutch Technological Top Institutes such as the Netherlands Institute for Metals Research and the Dutch Polymer Institute. It led to five EU programs with a strong Dutch participation. It also was responsible for the organisation of the first (ICSHM2009) and fourth (ICSHM2013) international conference on self healing materials and five international Summer Schools. The IOP program led to several new academic positions and new university courses on self healing materials, and many international collaborations. Finally, the IOP program led to new industrial products and markets and most importantly to vibrant academic-industrial networks.
We, the editors and authors of the 30 chapters, are convinced that this book will stimulate further development in this promising and highly attractive field of self healing materials. There are still many new concepts to be explored, existing concepts to be brought to a higher technology readiness level, legislation issues to be addressed and industrial experiences to be translated into improved versions of the first pioneering families of self healing materials before society can fully benefit from the full potential of self healing materials.
We trust the book will be a source of inspiration and reference for anyone with an interest in self healing materials for many years to come
Acknowledgements
The IOP Self Healing Materials program and this book would not have been possible without the contributions of many institutions and individuals. We acknowledge the crucial contribution of the Delft Centre for Materials (Delft University of Technology, Delft, The Netherlands) in opening the field and laying the conceptual foundation for this IOP program. During the entire program the Supervisory Board played a crucial role in guiding the development of the research and we thank its members Richard van de Hof (vice chairman), Jasper Michels (vice chairman), Ludo Aerts, Rinze Benedictus, Andre de Boer, Rolf van Benthem, Jan Bottema, Klaas van Breugel, Pieter Geurink, Jeff de Hosson, Gert-Jan Jongerden, Carel Kleemans, Cor Koning, Dick Koster, Henk Maatman, Jan Mijnsbergen, Ruth van de Moesdijk and Stephen Picken for their contributions and sustained commitment. The successive program coordinators Patrick van Veenendaal, Joris Vogelaar and Annette Steggerda-Batenburg made exceptional contributions to the smooth functioning of the program and solved many administrative issues. Finally, we thank all project leaders, industrial partners and the many postdocs and PhD students for their hard work and creative ideas. The excellent support from various departments of Rijksdienst voor Ondernemend Nederland (formerly known as AgentschapNL) during the execution of the IOP program is gratefully acknowledged too.
References
[1] S.R. White, N.R. Sottos, P.H. Geubelle, J.S. Moore, M.R. Kessler, S.R. Sriram, E.N. Brown & S. Wiswanathan, Nature 409 (2001) 794-797
[2] S. van der Zwaag, “Self Healing Materials: an alternative approach to 20 centuries of materials science”, S. van der Zwaag (editor); Springer, Dordrecht, The Netherlands (2007)
[3] S. van der Zwaag, N.H. van Dijk, H.M. Jonkers, S.D. Mookhoek & W.G. Sloof. Phil Trans Roy Soc A 367 (2009) 1689-1704
[4] “Self Healing Materials; concepts and applications”, NL Agency, The Hague, The Netherlands (reprint 2014)