
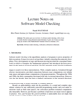
Aircraft design is a compromise of many different disciplines. Yet the history books are littered with projects that failed because something was overlooked in the early design stages that have come back to haunt it in the latter stages. This is very evident when it comes to evaluation of flying qualities and aircraft behavior as this is almost left out of the overall picture in the early design phases. It has long been considered that first order approximations are sufficient to indicate any issues in the early stages of design, but these can only show so much and are built on simplifications and approximations of a standard set of modes of motion. As airframes move away from classical designs due to improved materials, advanced manufacturing techniques evolve, or the improved efficiency associated with unconventional designs, so the approximations break down further. At this point it becomes prudent to perform more detailed assessment earlier in the project lifecycle. However, this too can have issues as it may be viewed that there is insufficient data, or the airframe is too complex to build a mathematical model. Then there is the question as to what to test and as such 6-DoF flight modeling is left until later in the process. This can have obvious consequences further down the project as 80% of the project and lifecycle costs are committed in the first 20% of the design. This immediately identifies that more effort should be put in the initial 20% to evaluate the complete design including flight modeling.
All the problems and issues that are presented above are now solvable through modern modeling techniques and software tools. This paper describes the tools developed to integrate flight simulation early on in the design process. Aerodynamics, stability and control estimates from the Advanced Aircraft Analysis software are corrected with the use of wind tunnel data, wind tunnel data is scaled to full size airplane and actual flight conditions. This data is then fed into the J2 Universal Toolkit to actually fly the airplane. Quality 6-DoF models can be built with minimal data and relative ease allowing engineers to start to look at running detailed analyses across multiple ideas and options very quickly and much earlier in the design process combining the more detailed handling qualities assessment with the aerodynamic evaluation, performance, propulsion and weight calculations right from the beginning of the design. Each point in the regulations has a configuration and maneuver associated with proofing compliance, these configurations and maneuvers can be set up in the modeling tool and all ideas and options can be evaluated. This very quickly identifies areas where the aircraft cannot get certified, and these ideas can then either be eliminated or modified. By following an integrated approach and implementing full 6-DoF flight modeling from the early stages of the design using simple methods initially, looking at sensitivity studies and the impact of tolerances throughout the process, and flying the complete certification envelope throughout the design provides a truly concurrent engineering approach to the design as all other disciplines feed into and have an impact on the behavior and flying qualities. This method allows more ideas to be evaluated earlier, enables the impact of changes to be tracked, and ensures that no surprises remain by the time the first flight comes around. This can reduce timescales, reduce the amount and cost of re-work to fix issues following flight test, and result in a better all-round design.
The paper shows the tools developed, the processes followed and an example airplane design using these tools.