
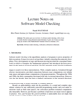
The maritime transport is guilty for about 2.5% of global greenhouse gases emission, since 940 million tonnes of CO2 are emitted around every year. Moreover, even though now the 96% of ships can be recycled, current recycling practices cause negative environmental impacts. Indeed, researches carried out on ‘ships graveyard’ showed a concentration of petroleum hydrocarbons 16,793% higher than at the control. Epoxy Fibres Reinforced Composites (FRCs) are sustainable candidates in this field. In fact, having the FRCs structures a light weight, fuel-efficient ships can be built. The global epoxy composites market size was valued at USD 25.32 billion in 2019 and is expected to expand at a compound annual growth rate (CAGR) of 6.2% from 2020 to 2027. In this sense, in the next few years, the market is expected to rapidly replace conventional materials with epoxy composites in several fields, including the marine one. However, concerns about their non-recyclability are rising more and more. In this study, by following a twofold “design for recycling” and “design from recycling” approach the chemical recycling process for thermoset polymer composites developed by Connora Technologies (California, USA) was considered as solution to overcome this issue. Moreover, the adoption of natural fibres, i.e. flax, and bio-based epoxy resin was used as environmentally-friendly solution to even avoid the use of petroleum based raw materials. To follow the first approach, i.e. “design for recycling”, Flax FRCs with bio-epoxy matrices were first produced via hand lay-up with vacuum bagging. Next, they were chemically treated to obtain a recycled thermoplastic (rTP). Then moving on the “design from recycling” approach, a reuse strategy was developed by exploiting the Electrospinning technique and producing electrospun fibers suitable for the interlaminar toughening of composite laminates.