
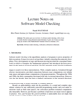
Tanks are commonly used to store various petrochemical products, water, etc., and therefore are considered a strategic infrastructure type and vital for social functions. Tank structural failure can cause significant life and financial losses and severe environmental damage depending on the content material. Thin-walled cylindrical shells can structurally fail in the form of buckling if the loading excessed the bearing capacity of the shells. FRP composites are a relatively modern construction material type. It has high stiffness and a high strength-to-weight ratio; therefore, FRP composites are also used for tank construction in addition to steel material. In this study, the buckling and post-buckling behaviour of steel and laminated carbon fibre composite (CFRP) cylindrical shells with different geometrical properties when subjected to uniform external pressure is studied numerically using Abaqus finite element software and Riks analysis. The results indicated that the buckling load of the shells decreased significantly with increasing the radius-to-thickness ratio (R/t) and radius-to-length ratio (R/L) of the cylindrical shells.