
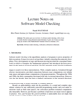
The reliable joining between two pipes is an important precondition and safe guarantee for the aviation pipeline system. In this paper, the inner swaging process is used to fabricate the aluminum alloy pipe joining components with large diameter and thin-walled structure to achieve the reliable connection of aviation pipes. The material of the joined pipe is AA5052-O, and the specification of the pipe is Φ75×t1.5 mm. The mechanical properties of the pipe were characterized for material modeling by the tension tests of arc-shaped sample cutting from the full-sized pipe. The whole model for the inner swaging process was simplified by fitting the cooperative motion of the mandrel, rollers, and cage into the independent motion of the rollers. Based on the above modeling process, the finite element model for the AA5052-O pipe forming process by inner swaging was established, and the accuracy of this model was verified by the comparison between the simulation and test results on the longitudinal section. Based on the numerical simulation results, the pipe filling into the grooves and deformation features were analyzed, and the forming process parameters were obtained. Finally, it is concluded that the qualified filling rate of the pipe into the grooves of the sleeve can obtain the reliable joining.