
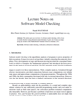
Laser drilling is used to produce micro holes in various components which have widespread applications in the automotive, aerospace and medical sectors. Many researchers have examined several ways to enhance the performance of this process by investigating different process parameters that seek to improve drilled hole quality. The productivity and cost of the laser drilling process are also important factors which need to be evaluated along with product quality. This research aims to investigate the characteristics of laser micro-hole drilling of IN 718 superalloy experimentally in terms of productivity (material removal rate (MRR)), cost (specific energy consumption (SEC)) and quality (hole taper). The results revealed that SEC increases with the increase in pulse energy and pulse width; furthermore, MRR increases with the increase in pulse energy and decreases with an increase in pulse duration. On the other hand, the opposite effect is observed for hole quality with the changes in process parameters. The optimal combination of process parameters is also found against the optimised response values (maximum MRR, with minimum SEC and hole taper).