
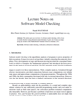
To implement Industry 4.0 (I4.0) in aerospace assembly, manufacturers need a practical method to review and quantify current build processes to determine the feasibility and provide insight into what tasks should be automated. Current literature reveals limited scientific means by which an aerospace assembly line can be examined for the viability of a transition to automated assembly. The aim of this paper is to present a digital tool which can be used to analyse engineering process data for a manual assembly line plan, providing a platform to assess what tasks are candidates for automation. The Engineering Process Records (EPRs) of an aircraft nacelle assembly were used. Data relating to task frequency and duration were extracted and nacelle part size, weight, and shape data was obtained from CAD files. These were translated into a process classification matrix in a Microsoft Excel spreadsheet. The creation and application of the tool enabled the distillation of assembly data to a point where outputs could be used to inform decisions around automation. Results show that 80% of the total time was consumed by only 20% of the tasks, hi-lighting these for potential automation. These tasks centred on drilling processes and the handling of fasteners. The high complexity/low volume nature of aerospace assembly means that although processes around making and dressing holes and the insertion of fasteners were candidates for automation, remaining tasks were of short duration or low frequency, where a transition to automated execution was less justifiable.